切削負荷のモニタリングによる切削時間短縮と生産性向上のメカニズム
2024.09.25 インダストリー4.0、ものづくり企業IoT、工場IoT、旋盤
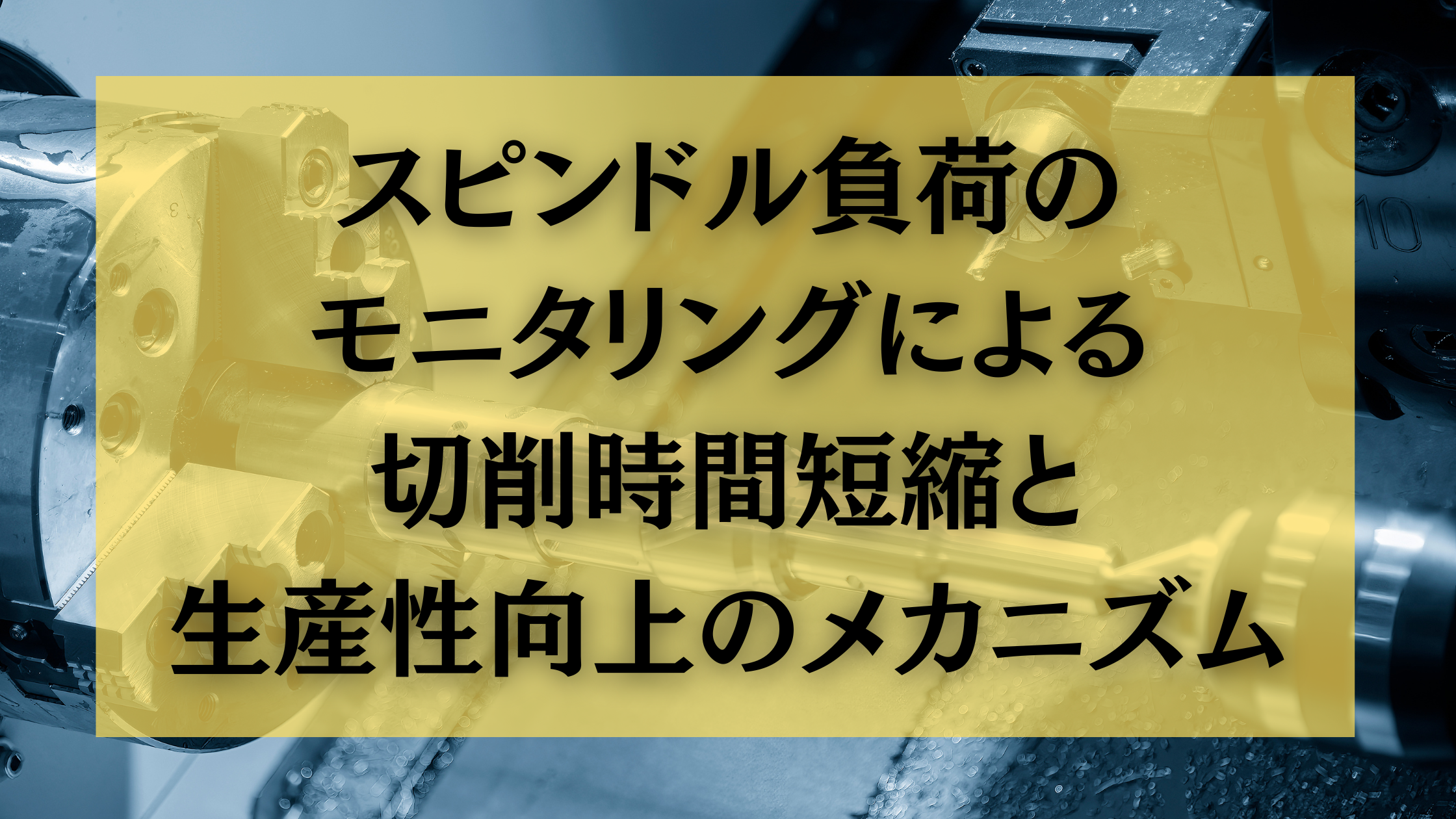
大阪市にある、小規模企業様では、FANUC Robodrillを用いてアルミ製の機械部品の加工を行っています。生産キャパシティを拡大し、より大きいマーケットに販路を拡大するために、シーメンスが提供するDXソリューションプグラムACMの導入を検討しました。ACMを用いて加工時間を分析したところ、後半の加工工程のうち実に60%がエアカットであることが判明。ACMによってこの時間を短縮することで、生産キャパシティを拡大させることを目指しました。
エアカットとは
エア加工とは、エアカットともよばれ、工作機械における加工において刃物が工作物を削っていない状態を表します。
工作機械で工作物を削る際、工具の刃先には大きな力がかかります。この力を調節し、刃先が痛むのを防ぎ、加工精度を保つためには、刃物の送り量の適切な管理が必要です。そのため工作機械の稼働時は、刃物が工作物に近づくアプローチ時や、刃物が工作物に触れていないときは刃物を素早く動かし、刃物が工作物を加工している間は加工条件に合った送り速度で刃物を動かすよう制御しています。
しかし実際には、工作物には素材寸法のばらつきなどがあり、工作物に向かってアプローチしていた刃物がどこで工作物に接触するか、厳密には分かりません。素材寸法がやや大きめだった場合には、刃物は予想よりも早く工作物に接触してしまいます。もしもこのとき、刃物がアプローチ速度で動いていたら、刃物は想定よりも早い速度で工作物に進入することになり、刃先に多大な負荷がかかります。それによって刃物の寿命が短くなることや、場合によっては刃物や工作機械を破損させる原因にもなりかねません。そのため、このような事態を防ぐために刃物が加工物に接触する少し手前から加工中と同じ条件で刃物を動かし、加工中と同じ状態で刃物が工作物に接触するようにしているのです。刃物が加工中と同じ条件で動きはじめてから、実際に加工が始まるまでの間。刃物が実際には工作物を加工していない状態をエア加工またはエアカットとよびます。
エアカットにはもう一つの意味があります。工作物を取り付けない状態で、実際の加工プログラムを実行し、刃物の動きを確認する作業です。これによりプログラムに重大な間違いがないかチェックしたり安全を確認したりします。しかしこの記事におけるエアカットとは、刃物が工作物を削っていない状態を意味しています。
エアカットは、工作機械や刃物を守るためには欠かせない動作です。しかし一方で、エアカットによって生じる課題もあります。それはサイクルタイムの増加です。エアカットは必要ですが、実際に工作物を加工しているわけではありません。そのためエアカットの時間が長くなれば、それだけサイクルタイムを長くしてしまうのです。
この課題を解決するためには、エアカットの時間を最小限にしなければなりませんが、一方で加工素材の寸法のばらつきもあります。それに対応し、エアカットの時間を短くするためには、定量的な制御ではなく、加工状況に応じた制御が必要になるのです。
FANUC Robodrill
お客様の所有されているFANUC Robodrillは、FANUC製の切削加工機で、小型で高速、高精度、高効率なのが特徴です。FANUCはFA機器やロボットの他に、小型切削加工機や電動射出成形機、ワイヤ放電加工機などを製造しており、この中の小型切削加工機をRobodrillと称しています。主軸30番の軽さを活かした主軸ユニットと、高剛性の機械構造、さらに高速な加工を実現しつつ、高精度、高出力の加工を実現しています。
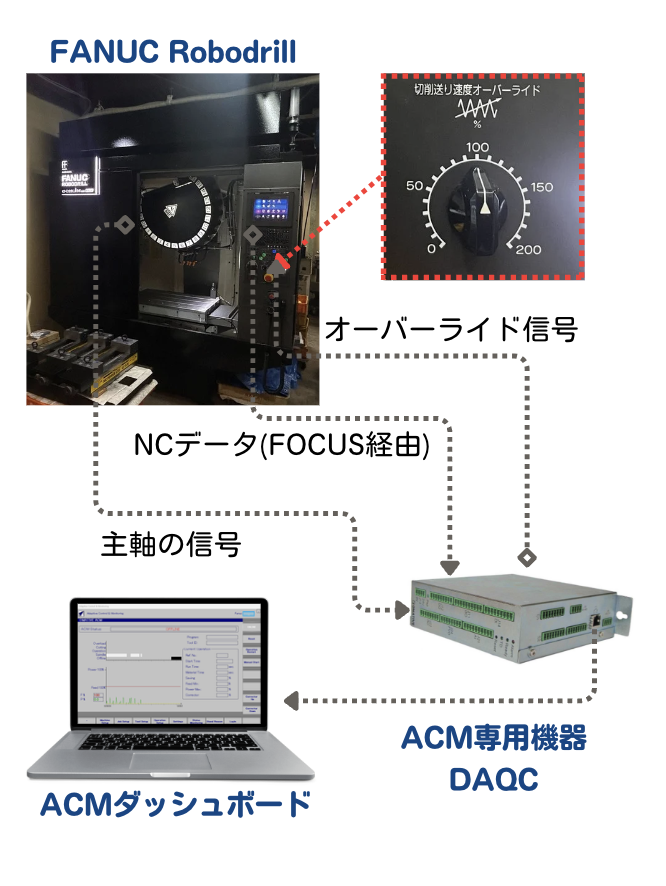
FANUC Robodrillのもう一つの特徴が、高い稼働率です。「壊れない、壊れる前に知らせる、壊れてもすぐ直せる」をテーマに、信頼性を重視した開発を行っており、FANUC社内加工工場にて200台以上のRobodrillを24時間稼働させています。それらから得られた稼働データや保守情報を設計にフィードバックすることにより、より高い信頼性を確保しています。
FANUCではRobodrillの他にも自動化用のロボットなど、多くの製品を作っているため、ロボットを使った自動化にも対応しやすくなっています。Robodrillには、オプションでロボットインターフェイスを取り付けることが可能で、ロボドリルとロボットをかんたんに接続できます。
今回の事例では、FANUC Robodrillを使いつつ、デジタルトランスフォーメーション(DX)を活用しながら生産キャパシティを拡大するのが目的でした。そこでシーメンス(Siemens)が提供するDXソリューションプログラムACMを採用することになりました。左図はFANUC RobodrillとACMとのハードウェアの連携仕組み。
ACMの仕組み
ACMとはAdaptive Control & Monitoringのことで切削中のスピンドルの負荷を常時モニタリングし、刃物の送り速度を適切に自動調整するソリューションです。たとえば、刃物が材料に進入する場面や、切削量が増えるなど、刃物に大きな負荷がかかる際には、刃物の送り速度を自動的に下げます。一方で比較的負荷が低くなる場面や、エアカットの場面では送り速度を上げます。このように、スピンドルの負荷を常時モニタリングしながら送り速度の制御を行うことで、従来のような加工プログラムによる定量的な送り速度で加工するよりも、効率のいい加工が可能になります。
ACMで行われるコントロールは、主に次の6つです。
1.アプローチから切削開始点までのエアカット時間短縮
2.切削開始時は工具保護のため送り速度を減速
3.主軸の負荷に応じて送り速度を変化させる
4.主軸の負荷が大きくかかるポイントでは、工具の破損を防ぐため、送り速度を下げる
5.主軸の負荷に応じて送り速度を変化させる
6.エアカットなど、負荷がかかっていないポイントでは送り速度を上げて、加工時間を最小化させる
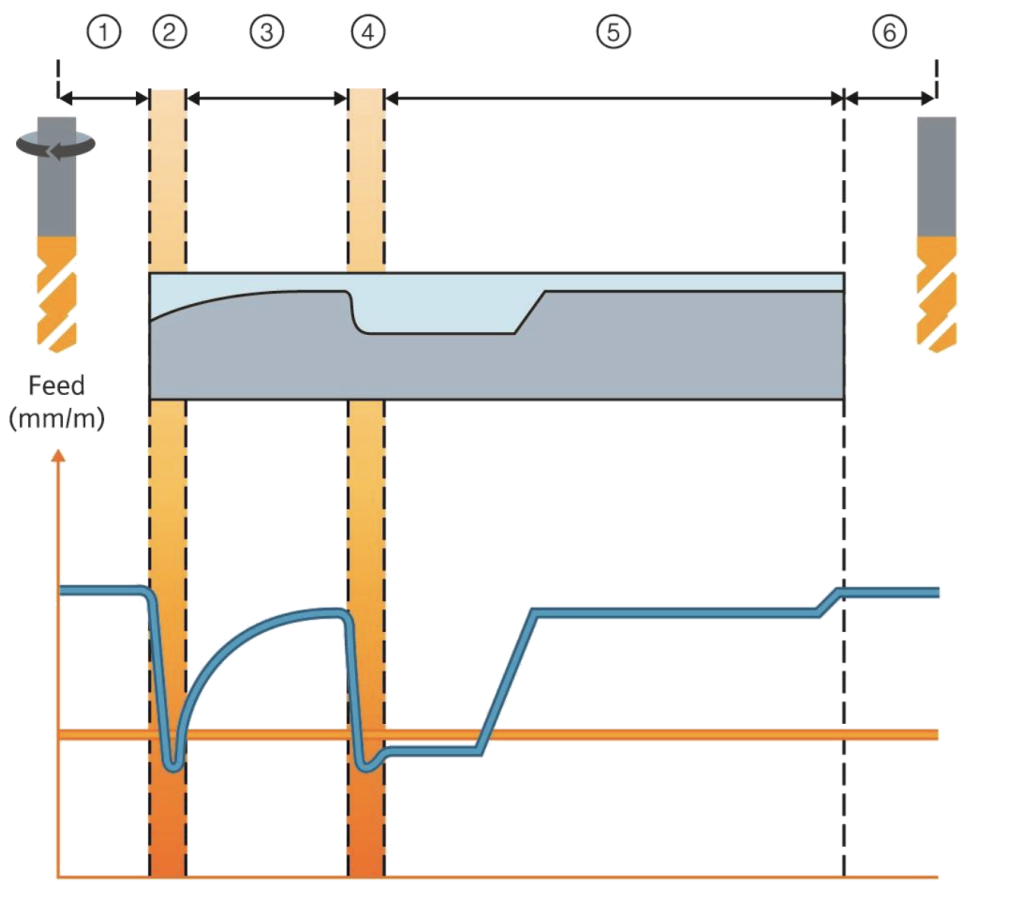
一般的に工具の衝突を防止する際には、その加工フェーズにおける加工速度を落とすため、その部分においてはエアカットであっても刃物の送り速度が低下します。しかしACMを導入すれば、主軸の負荷を検知して自動で速度を調整するため、エアカットの送り速度を下げなくても工具が工作物に衝突するのを防げます。また負荷に応じた送り速度を自動で選ぶため、工具寿命も向上するのです。
今回のケースでは、後半の加工工程のうち60%がエアカットでした。ACMを導入することで、エアカットの送り速度を従来よりも早くし、アプローチの速度を上げることができるようになりました。そのため、従来は2分30秒かかっていた工程を1分59秒まで短縮でき、合計で20%の加工時間の削減になったのです。これにより、機械の生産キャパシティが大幅に向上。工場の移転、拡大や、新しい生産設備を導入することなく、工場のキャパシティを拡大することに成功しました。
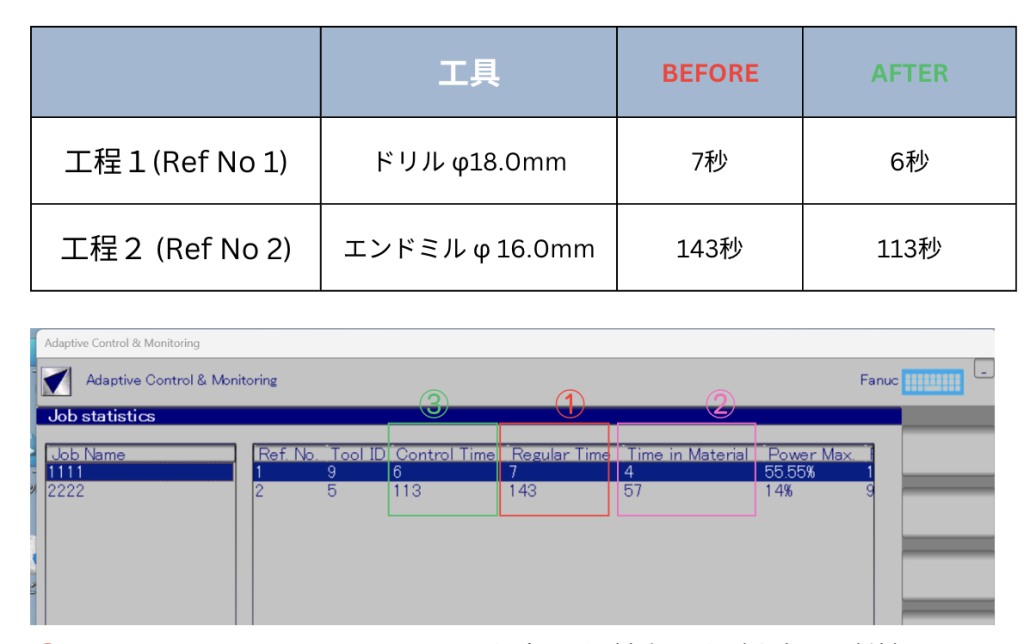
今回のケースでは、後半の加工工程のうち60%がエアカットでした。ACMを導入することで、エアカットの送り速度を従来よりも早くし、アプローチの速度を上げることができるようになりました。そのため、従来は2分30秒かかっていた工程を1分59秒まで短縮でき、合計で20%の加工時間の削減になったのです。これにより、機械の生産キャパシティが大幅に向上。工場の移転、拡大や、新しい生産設備を導入することなく、工場のキャパシティを拡大することに成功しました。
ACM導入機械のデモンストレーションを現場でご覧になれます
見学場所 | 守口市大阪府 |
---|---|
実施期間 | 2024年10月1日~2025年8月30日 |
見学時間 | <午前> 10:00~12:00 <午後> 13:00~16:00 ※完全予約制 |
定休日 | 土曜日・日曜日・祝祭日・夏季休暇 |
人数 | 5名様 まで |
費用 | 無料 |
申込方法 | Email:申込フォームより申込 FAX:申込フォームをダウンロード |
申込受付期間 | 希望日の2週間前まで |