潤滑損失条件下で作動する歯車のためのIn-situ 摩擦測定を用いたオイルオフ特性化法
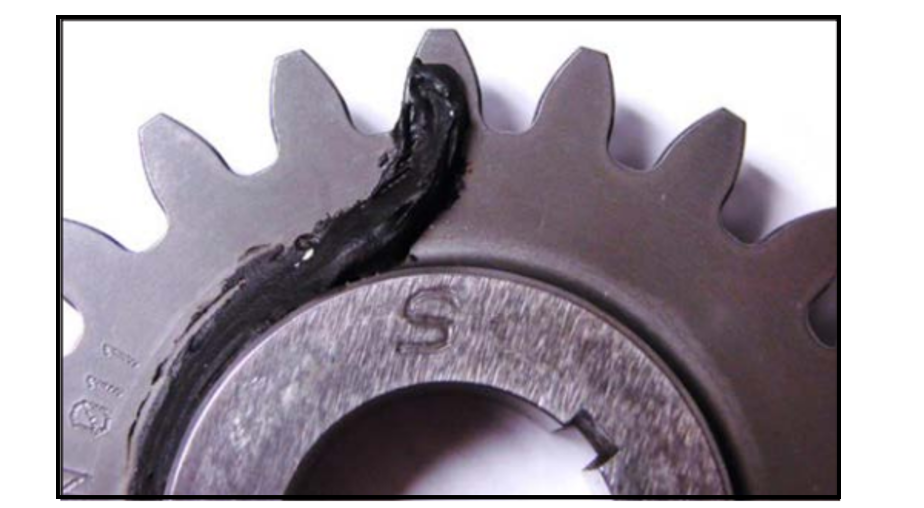

著:Aaron C. Isaacson、Matthew E. Wagner
前書き
ギアのオイルオフ(潤滑損失またはオイルアウトとしても知られる)性能評価は、国防総省およびさまざまな回転翼航空機製造業者にとって非常に興味深いものであり、それに起因して、航空機はアクシデントによる潤滑油損失状況において安全に着陸することができる。しかしながら、早期の検出が可能であるピッチングまたは曲げ疲労のような典型的なギア故障モード(*JIS C5750-4-3:2011では「アイテムにおける故障の様子」と定義されている。)とは異なり、オイルオフの状況におけるギア故障は非常に急速であり、壊滅的である可能性が高い。故障は急速にトルク伝達の喪失および航空機の制御不能をもたらす。
潤滑ギアボックス性能損失テストに対する関心は最近のものではない。 1978年、HudginsとSchuetzは、ベトナム紛争での戦闘被害による潤滑油の損失に基づくヘリコプター駆動システムの残存性向上の必要性を説明している(参考文献1)。彼らは、故障までの典型的な時間は5〜9分であり、故障モードは矛盾していると述べた。 つまり、5〜9分で航空機が不良環境を脱出し、安全に着陸するのに十分な時間ではないということである。潤滑システムの故障後30分の運転の必要条件が確立され、今日まで使用されている。連邦規則のタイトル14コード:耐空性基準(参考文献2)。
現在のヘリコプターやティルトローターは、長距離など、掘削リグや空母へのアクセスのための潤滑油の損失が30分未満のミッションに一般的に使用されている。これはこの長年のベンチマークの見直しにつながっており、規格は現在改訂中である。フルギアボックスの残存時間テストは36分から67分の間になり、さらにテストを繰り返す必要があることが示されている。
関連研究
1978年から2010年代初頭にかけて、NASAグレン研究センター(参考文献3)とカマン・エアロスペース(参考文献4)(どちらも補助油の供給によるギアボックスの性能向上に焦点を当てている企業)が行ったいくつかを除いて、公開文献に報告されているオイルオフテストに関連するものはほとんどなかった。補助油供給による変速機性能の改善に関する研究多くの教訓があるが、最も明白なのは、テストの結果に影響を与える可能性がある多数の変数があり、最小限の潤滑でギアボックスが長時間作動する可能性があるということである。
利用可能なテストレポートの多くは、本格的なギアボックス用(参考文献1、4–8)であり、複雑さは驚異的である。各テストの結果に影響を与える可能性がある変数は次の通り、ギア配置(惑星対非惑星)、ギアバックラッシュ、ギア素材、ハウジング設計(オイルをプールするための場所の提供)、オイル漏れの種類(圧力損失、油溜めの穴)、ベアリングとシャフトの隙間、ベアリングタイプ、ベアリング材料、摺動面の表面粗度。ミストを発生させる能力、伝熱性など。ギア関連の変数を最適化するためのコンポーネントレベルのテストが、コストのかかる本格的なテストを実施する前の貴重なステップであることは明確である。
歯車かみ合いへの潤滑損失の側面をモデル化するために、いくつかの計算ツールが構築されている(参考文献9–15)。最も洗練された方法は、おそらく接触力学の様相を取り入れた、McIntyreらによって取られたマルチフィジックスベースのアプローチであろう。接触力学、摩擦学、ギアボックスフローの計算流体力学モデリング、ギア内の伝導、ハウジングとコンポーネント、および環境への自由対流の側面を取り入れている(参考文献14)。このモデルは、NASAグレン研究センターのコンポーネントテスト装置を基にしており、歯全体の温度分布と故障までの時間を予測する(参考文献13〜14)。モデル出力をペンシルバニア州立大学で収集された気温データと相関させるための取り組みが現在進行中である。現在利用可能なモデルでは、確かに有用な観察はできるが、次のようなオイルミスト変化、テストの間に発生する炭素質酸化堆積物、ギア歯形損失と他の未知の影響のような変数を説明することができないのである。
ギア損傷メカニズム
ギアボックス内部の潤滑剤は、金属表面を分離し、この滑りによって発生する熱を分散させて除去するという2つの主な機能を果たしている。潤滑剤の供給がなくなると、部品はすぐに加熱され始める。これにより、残った油膜が薄くなり、金属同士の接触が速やかに起こるため、それに伴って摩擦が急激に上昇し、摩擦が増加するとより多くの熱が発生、問題が悪化する。オイルがないと、システムは熱放散のためにギアボックス内外の部品間の伝導と対流に依存している。報告されているテスト結果の大部分は、ギアボックスが設計温度よりも高い温度で動作している、潤滑油が失われた後の準安定熱平衡期間を示している(参考文献3、5、15–17)。歯車の歯は、故障する最初の要素であるとしばしば報告されている(参考文献1および7)。金属と金属が接触するとすぐにこすり始める(潤滑剤皮膜の破壊)。高熱は最終的に鋼を軟化させ、荷重下で塑性変形を引き起こしてしまう(参考文献18)。極端な温度はまた熱膨張をもたらし、それはバックラッシュが不十分である場合に歯車の焼き付きを引き起こす可能性がある。ギアバックラッシュは通常、オイルオフの際に予想される高温を考慮して増加させることが可能である。

スカッフィング
前述の研究では、スカッフィングがギアのオイルアウト不良プロセスの重要な部分であることが確認されている(参考文献1、3、5、7、9-10、15、17-19)。スカッフィングは、弾性流体潤滑(EHL)メカニズムの物理的な失敗である(参考文献20)。それは、不十分な潤滑による反復的な溶接および表面凹凸の引き裂きとして説明することができる。耐摩擦性は伝統的に、潤滑剤にEP添加剤を使用すること、または接触面間の摩擦を低減する他の手段(例えばコーティング)により表面仕上げを改良することによって高められてきた(参考文献20)。
多くの研究者によるクーポンレベルテスト(*機械的応力負荷による材料の強さの調査)を使用して、スカッフィングは研究されてきました。ピンオンディスク、四球、ブロックオンリング、ツインディスク、ボールオンリング、ボールオンディスク(*すべて摩擦摩耗試験方法)は、制御された特定の試験条件下でスカッフィングを生じさせるために使用され(参考文献19)、粗さ、オイル添加剤などの影響を定量化できる。米国陸軍研究所とWedeven Associates株式会社の両方で、潤滑油の損失性能を評価するためにボールオンディスク試験を使用して行われた重要なものがある。スカッフィングが主要な故障メカニズムである一方で、いくつかの性能上の違いが存在し、継続的な研究の主題となっている。これらの違いはおそらく、インボリュート歯車の歯の幾何学的形状に固有の応力変数および滑り変数、ならびに歯車の歯の噛み合い作用が、最少量の残留潤滑剤ミスト(または蒸発した炭素さえも(Ref. 21))継続的な潤滑をもたらすことを可能にするという事実に起因する。
スカッフィングの失敗は、テストの種類にかかわらず、一貫した特定の論証を示している。Yagiらによる「マイクロスカッフィング」と呼ばれるスカッフィングの開始後には安定段階が続いた(参考文献22)。この段階中に発生していることは、試験の種類、滑り率および存在する残留潤滑剤の量に応じて変わる。それは、残留潤滑剤と金属の高温での酸化によって引き起こされる酸化的摩耗現象(参考文献23)である可能性が最も高く、結果として接触体間の摩擦を減少させる高炭素堆積物をもたらしている。これが準安定熱平衡が起こる理由である。この段階の長さはいくつかの要因に依存するが、システムが発生した熱を接触からどれだけうまく吸収して除去できるかによって本質的に決まる。やがて温度は克服するには大きすぎるほど上昇し、摩擦と温度が急激に上昇するところで別の移行が起こり、壊滅的な故障につながってしまう。(参考文献19、22–24)。
ギアテスト
クーポンテストと本格的なギアボックステストの間にはギャップがあり、部品レベルのテストを使用して、より現実的で費用対効果の高いオイルアウトスクリーニング試験を実行できる。 これらの試験は現在、最先端の歯車鋼、表面処理、潤滑剤、さらにはオイルアウト作業用のノンインボリュート歯形の性能上の利点を評価するために使用されている(参考文献17および25)。 残りの文章では、オイルアウト性能の特性評価のために開発された試験装置と手順について概説しよう。
テスト装置ハードウェア
本稿で説明するオイルオフテストには、最大10,000 RPMの速度が可能な3.5インチの中心距離駆動型再循環4平方試験装置を使用している。この試験装置は、4平方ループに油圧でトルクをかける専用の反転ギアボックスを使用する。 (試運転中のトルク変化システムの概略レイアウト、図1)。オイル除去作業を可能にするために、テスト装置にいくつかの変更を加える必要があった。
給油システムの変更
通常のオイルオンテストでは、テストギアボックスはジェット潤滑を使用してテストギアにオイルを供給している。さらに、テストギアシャフトは、加圧油供給を必要とするベアリングによって各端部で支持されている。 テストボックスのベアリングは、潤滑のために歯車かみ合いに供給されるのと同じオイルを使用し、ベアリングはテストボックスの内部に排出される。 テストボックスベアリングへの潤滑を維持しながら、歯車かみ合いへのオイルの流れを遮断できるように、リグの給油システムを変更する必要があった。 オイル供給ラインを有するテストボックスにはニードルバルブも装備されているので、オイルオフ中のテストボックス内のオイルミストが同一であり、テスト間で再現可能であることを保証するためにベアリングオイルの流れを制御できる。 試験中、ベアリング温度限界を継続的に監視して、適切な動作を確認できた。
オイルコントロールシュラウド
試験装置はまた、潤滑剤の流れが停止した後に残留油を制御するために試験装置の周囲を囲むように修正された。 シュラウドは示された設計(参考文献9)に基づいており、シュラウドから歯先までの半径方向の隙間は0.06インチであり、各端面までの隙間は0.06インチである。 ギア回転から半径方向外側に配置されたスロットは、オイルオフ中に残留潤滑油を排出することを可能にする。 (組み立てられたシュラウド、前面カバーが取り付けられていない状態が示されている、図2)

かみ合い外温度試験
測定直径0.125インチのかみ合わない熱電対を、示されている位置(図2)に、オイルオフシュラウドに組み込んでいる、回転する歯車の歯にできるだけ近い軸方向に配置した。オイルの侵入中は、メッシュの油温が測定されるが、オイルの除去中は、ギアの歯の表面近くの同伴空気の温度を測定するためにも使用されている。 温度傾向は、オイルオフ中のギア故障の進行を監視するための貴重な測定基準であることがわかった。
摩擦測定
示されているように(図1)、試験装置はまた3つのトルク変換器を備えていた。 2つのトランスデューサが4つの四角形のループ内のトルクを監視し、追加のトランスデューサが駆動モータからの入力トルクをモニタする。次に、これらの測定値を使用してテストボックスと反転ボックスの摩擦損失を計算する。損失計算および摩擦測定技術の詳細は以前に著者らによって提示されている(参考文献26)。 テストボックスの摩擦損失測定値は、オイルオフの破損への進行を監視するための最も効果的な測定基準であることが判明した。また、壊滅的な破損時のかみ合い外温度測定傾向とよく相関することもわかった。 著者の知る限りでは、オイルオフギア試験中の歯車かみ合い摩擦のIn-situ測定は、これまで公開文献に報告されていない。

テスト手順
オイルオフテスト手順は次のように定義されている。
1.慣らし運転ステップ#1:慣らし運転トルクで30分間オイルを入れたまま走らせる。
2.ステップ2の慣らし運転:トルクをテストするために急上昇し、60分間オイルで運転し続ける。
3.オイルオフ:テストトルクで運転を続け、オイルを切る。 壊滅的な障害を監視する。
4.振れ:振れ制限時間(通常30分)に達したら、オイルを入れてトルクを上げる。
5.安定させる:オイルで10分間トルクレベルを上げて運転する。
6.繰り返し:オイルオフを繰り返し、振れ制限時間まで走り続けさせる。 必要に応じて、壊滅的な障害が発生するまで手順4〜6を繰り返す。
典型的なテスト結果
テスト条件の厳しさに基づいて、オイルオフの結果は通常、表1にまとめられた4つのケースのうちの1つに分類されることがわかった。各ケースの詳細と例を以下に示そう。

ケースI:スカッフィングなし。 最も軽度の場合、ギアの歯が擦り切れることなくオイルオフテスト期間を続けることができる。これは、テストボックス内の残留オイルミストまたはテストトルクが小さすぎることが原因である可能性がある。この状態は頻繁には発生しないが、スカッフィングの発生が検出されたときの摩擦損失とメッシュ外温度の傾向を説明するためにここに提示されている。
図3は、同じ歯車対を用いてトルクレベルを上げて行った4つの試験を示す。これらのテストは、摩擦損失とメッシュ外温度の効果を評価してスカッフィングを検出するための初期開発作業の一部であった。 各トルクステップ後に目視検査のために試験を停止し、そして500、600および700lb-in段階ではスカッフィングを全く示さなかった。 これは、残留潤滑剤および/またはトライボロジフィルムがこれらの条件下でのスカッフィング開始を防止するのに十分であることを示している。
ケースII:壊滅的な故障まで進行させずにスカッフィング。 図3では、800 lb-inまでテストを続けると、摩擦と温度の両方の傾向に大きな変化が見られ、目視検査でこのトルクでスカッフィングが発生したことが確認された(こすり傷の付いた歯の表面が示されています、図4)。 典型的な試験手順では、この試験は壊滅的な故障または振れを続けることが許されていたであろうが、摩擦および温度傾向が、スカッフィングが起こったことを示した後にこの試験は中止された。この試験結果は、摩擦およびかみ合い外温度を使用してスカッフィングの開始を検出することの有効性を実証している。

状態がさらに厳しさを増すにつれて、スカッフィングは通常、油の流れが止まった後に急速に起こる。 これは図5の摩擦損失の傾向に示されており、これはオイルオフの直後にピークに達する。発熱は摩擦と共に増加するので、これはかみ合い界面での最大発熱がオイルオフ直後のスカッフィング事象中に起こることを示唆している。 最初のスカッフィングの後、テストの実行を続けるにつれて摩擦損失とかみ合い外温度は安定します。この場合、条件はテストを壊滅的な故障へと進行させるほど厳しいものではない。

かみ合い外の温度が漸近的な場合、準安定熱平衡になる。 暴走障害が発生する前に、かみ合いの入熱がシステムから吸収および除去されている。 歯の表面はこすり傷がついていますが、それでも歯車はトルクを伝達しているので、このテストでは故障とは見なされない。テストは、壊滅的な故障に進行することなく、ギアが数時間の間、擦り切れたオイルオフ状態で動くことが可能であることを示した。ランアウトタイムリミットに達すると、オイルが再びオンになり、トルクが増加して次のオイルオフステップに備える。
ケースIII:壊滅的な故障への進行を伴う擦り傷。 ケース2よりもテスト条件の厳しさが増すと、テストは最終的に壊滅的な故障へと進むでしょう。壊滅的な故障の2つの異なるケースのトルクと温度のデータのプロットが示されている(図6)。 ケースIIIの故障進行とともに、スカッフィングによる最初の摩擦ピークの後には安定した運転期間が続く。 壊滅的な故障に移行する前の安定した動作のこの期間は、異なるテストグループのパフォーマンスの分離を可能にする。
ケースIIIでは、安定した動作期間の後に摩擦が再び増加し始める。これは、テストが壊滅的な故障に進行していることを示す。壊滅的な破損が始まると、メッシュ外の温度変化率も増加する。典型的には、摩擦が増大した直後に動力伝達の完全な喪失が起こり、この程度まで進行する歯車対の例が図に示されている(図7)。動力伝達の完全な損失に対する試験は試験装置に損傷を与える可能性があるので、摩擦とかみ合い外の温度傾向に破滅的な故障が差し迫っていることを示唆すると、試験は通常停止される。送電喪失前に停止したテストの例を図に示す(図8)。 また、歯に著しい塑性変形があることに注意すること。



ケースIV:即時の壊滅的な故障。 試験条件がケースIIIよりさらに厳しさが増すと、図6のケースIVとして示されるように、オイルオフ直後に壊滅的な故障が発生する可能性があります。この進行では、ケースからの最初のスカッフィング後の安定したオイルオフ操作の期間 IIIは存在しない。この場合、テストグループ間でパフォーマンスを区別することは困難であるため、即時の壊滅的な故障は望ましくない。
理想的なテスト条件
理想的なテスト条件はケースIIIの壊滅的な故障の大部分を確立されたテストトルクで生み出すはずです。試験手順によれば、振れが生じた場合(ケースII)、トルクは増加され、そしてオイルオフ事象が繰り返される。これは結局、確立された試験トルクよりも高いトルクで壊滅的な故障を招くであろう。 壊滅的な故障を起こすには複数のオイルオフ事象が必要となるため、振れの数を最小限に抑えるのに十分厳しいテストトルクを選択することが望ましい。同時に、試験トルクは、有用な性能データを生成しない即時の壊滅的な故障を引き起こすほど高すぎてはならない(ケースIV)。
ロードステップ研削テスト。ケースIIIの壊滅的な故障の大部分を引き起こすテストトルクは、テストプログラム間で異なり、ギア設計、オイル選択、表面仕上げなどの要因によって影響を受ける。 最小数の試験ギアを使用して試験トルクの近似値を確立するために、ロードステップアプローチが使用される。これは、10分のオイルオンと10分のオイルオフのより短い時間間隔が使用されることを除いて、前に概説した試験手順と同様である。装置の能力の下限に近いトルクが始動トルクとして使用される。これは、10分のオイルオフ後に100 lb-in増加し、壊滅的な故障は発生しない。典型的なロードステップ検索テストの一部を示そう(図9)。

ロードステップ検索試験は典型的には壊滅的な故障が起こる前に試験ギアを複数のオイルオフ事象にさらすため、この方法によって決定されるトルクは使用すべき最終テストトルクではないかもしれない。しかしながら、それはテストトルクを直ちに検出し、オイルオフを受けた新しい歯車が所望の故障に進行することを確認する、さらなる試験のための出発点を確立するであろう。
収集された追加データ
騒音と振動の測定。試験中に騒音および振動のデータも収集した。 提示されたデータ(図10〜11)には51.2 kHzのサンプルレートが使用されている。この場合は、歯の噛合い基本周波数の4次高調波までとなる。
図10は、非研磨メディアを用いた等方性表面処理(ISF)探傷面を使用して実施された2つの試験の加速度計データのRMS振幅を示している。加速度計データは、摩擦測定データと同様の傾向を有することが示されている。スカッフィング事象中の最初のピークの後には安定した動作期間が続き、試験が壊滅的な故障に移行するときに第2の増加をもたらす。
同じテストからのデータが、オイルオフの前後両方の図11の周波数領域に示されている。
予想通り、FFT(高速フーリエ変換)データの歯と噛み合う基本周波数と高調波のピークは、オイルオンブレークイン時に表示されます。 壊滅的な故障への進行は、歯の輪郭が激しい擦り傷から悪化するにつれて、追加の側波帯の出現を示す。


歯の熱電対データ。噛合い外れの同伴空気温度を歯車の歯の表面動作温度と相関させるために、熱伝導性エポキシ(樹脂)を使用して歯車の一方の歯の側面に熱電対を装備した(図12)。 図13は、オイル切れ試験の摩擦損失の結果を、噛合い外熱電対データと歯の側部熱電対データとともに示している。 歯の側面温度は初期最高値を示し、その後、定常状態近くまで徐々に低下する(熱平衡)。 これは、メッシュ境界面での最大熱発生が、オイルオフ直後の摩擦ピークによって示される最初のスカッフィング事象中に生じるという理論を検証する。この特定のテストは壊滅的に故障することはなく、オイルなしで90分以上走ることができた。 試験が終了したときに、歯の側面で約440°Fの定常状態温度が測定された。
図14は、壊滅的に故障したテストの歯の側面の熱電対データの例を示している。故障開始時には、かみ合い外温度で観察された傾向と同様に、歯の側面温度の変化率が増加する。試験が終了する前に、700°Fを超える歯の側面温度が測定された。 このデータは、潤滑剤喪失事象の計算モデルを検証するのに有用であり、その例は(図13および図14)に見出すことができる。



適用例:実験群とベースラインの比較。 テストグループ間で性能を差別化するこのテスト方法の能力の例を表2と図15に示す。ベースライン試験群および高度な材料、コーティング、および油を用いた第2の試験群によるオイルオフ試験の結果が示されている。オイルオフ性能試験データのばらつきが十分に文書化されているので、複数回の試験反復を使用した(参考文献1、5、10、17および27)。 表2に示すように、実験群のデータにはばらつきがあるが、すべてのケースでベースライン群と比較してパフォーマンスの大幅な向上が見られる。
図15は、2つのテストグループ間の摩擦と温度の傾向の違いを示している。実験群は、オイルオン条件およびオイルオフ条件の両方においてかみ合い外温度の低下と共に、スカッフィング開始の遅延および壊滅的な故障へのより遅い進行を示す。


概要
提示された試験方法とデータは、歯車の噛み合いにおける摩擦損失と噛み合い外の温度が、潤滑が喪失した状態での航空宇宙用歯車の動作と性能を評価する有効な手段であることを示しています。具体的には、歯車の噛み合い摩擦は、オイルオフ事象中のスカッフィングおよび壊滅的な破損への進行の敏感な指標であることが示された。このホワイトペーパーで説明されている取り組みは、ギアのオイルオフ性能を評価するための実験的方法論を提供する。これは、その壊滅的で突然の性質のために過去に特徴付けることが困難であった。典型的な故障は、試験条件の厳しさに基づいて4つのカテゴリのうちの1つに分類されることがわかり、望ましい故障の進行を確立するためのガイドラインが提案された。ベースライン試験グループおよび実験的試験グループからのデータの例は、オイルオフ条件における先端材料、コーティングおよび潤滑剤の性能改善を強調するための試験方法の能力を実証している。
現場でお困りの方を
徹底的にサポートします!
ソリューション、製品に関する
お見積もり・お問い合わせはこちらから
まずは、お気軽にご相談ください!
当社への貴社商品・サービスのご紹介営業につきましては、お問合せ・ご相談フォームにてご連絡下さい
- TEL
- 078-335-7573 営業時間 : 9:00〜17:00(平日)