IoTで加工作業の効率アップ?!見えないムダを削減する実例とポイント
2021.03.29 インダストリー4.0、基礎
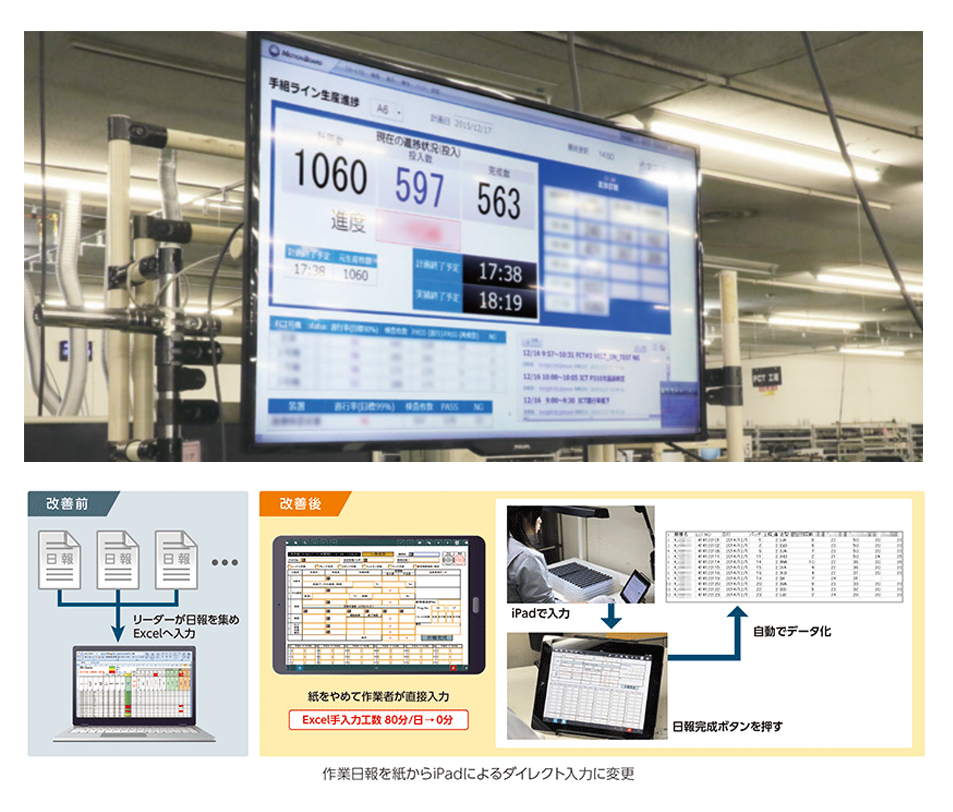

引用: 富士ゼロックス株式会社様
前回の記事ではIoTを用いたユニークなアイデアを紹介いたしました。
機械製造の分野でも、IoTで機械加工状況のデータを集めたり、日々のメンテナンスなどで、工場設備の歯車などの摩耗状況といった、整備に必要なデータもセンサを使って取得できるようになります。
こうしたIoTを活用した業務効率化を考えようとしても、構成ややり方は理解できていても、それを導入しても一体どれぐらい効率化ができるの?という素朴な疑問を持っている工場経営者の方も多いのではないでしょうか?
今回は実例を用いて、機械加工などの製造業へのIoT導入を考えます。
どんな無駄を削減するためにIoTを導入するのか?
まずは、IoTを導入する目的をはっきりさせる必要があります。
前回のIoT事例においても、ただ「センサを取り付けて、モニタができるようになった」という状況から一歩進んで「モニタできる状態を使ってどうするのか?」ということで、新たなビジョンが生まれています。
IoTを導入し、モニタすることでどのようなことを行うのか?ということを突き詰めて考える必要があります。日頃こんなことができたら便利なのに、というレベルのアイデアから、こんなセンサを導入したらモニタ出来るところがこれだけある、などいうものまで様々な視点から考える必要があるでしょう。
IoTを導入してからの利用目的と効果の検証を行うことこそ、IoTを導入してよかったと思える下地を作ることになります。
汎用品の組み合わせで構築した安価なIoTでモニタを行い検証する
IoTを導入するとなると漠然とお金がかかるのでは?と考えている方に見てもらいたい実例があります。
愛知県で自動車向けの樹脂製品などを製造する日進工業では、IoTを自社オリジナルで構築をしたことで安価なIoTシステムを実現しました。
どのような内容のことを行ったのかというと、製造現場が主体となって汎用品の組み合わせでセンサからクラウドサービスへの接続システムやモニタまでを構築したことで、非常に安価なシステムを実現したということでした。
例えば、センサに接続されるクラウドサービスへの接続機器にはラズベリーパイのような汎用品のコンピュータを用いました。モニタ用のスマートフォンなども中古の機器を接続するなど、低コストの実現に向けて努力をしてきました。
生産ラインに掲示される故障率などを表示する全体ディスプレイも中国製の安価なものを選定して構築にかかる費用を可能な限り削減しました。
安価な分、自分たちで構築する範囲が増えるがメリットもある
IoTというと専門業者にお任せすると考えている方も多いでしょう。
素人目に見てもその方が安心ができるし、何か購入部品の仕様が間違っていて、最悪の場合、買いなおしとなってしまうようなことを防ぎたいと考える気持ちも分かります。
しかし、すべての権限を専門業者に任せてしまうデメリットもあります。それは、IoTを構築する費用が高くなるというだけではありません。
仮に専門業者にお任せをしてIoTシステムを構築した場合、完成後の運用時にアップデートをしたいと考えても、専門業者の作業が必要など、運用にかかる費用も高くなる可能性があります。
また、システムが止まってしまった場合、ブラックボックスで構築されてしまった場合、自分たちで復旧することが困難となってしまい、そのたびに業者対応が必要となる可能性もあります。
IoTによる必要な情報がどれなのかということを把握しているのは他でもない現場の担当者の方々です。
こうした人たちが自分の手でIoTを構築し、運用での改良も自分たちの手で出来たほうがより良いシステムとなっていくことが分かります。
設備稼働率が10%上昇 工場の状態を見えるようにしたことで分かった無駄
日進工業の例では、設備の稼働率や、オイル注入などの工場内の定期整備による待ち時間などを見えるようにしたことで、減らすべき無駄な時間が分かるようになったと言います。
また、その結果を見て、現場の生産ラインの担当者が様々な無駄を削減するアイデアが活発に出るようになり、改善の結果も全体で共有することができるようになりました。
工場での設備の稼働時間や様々なデータがリアルタイムで分かるようになったことで、設備稼働率が80%から90%に上昇したという結果を得ることができました。
こうしたシステムを導入し、見えるようになったことでシステム側も改善しなければならないことというものも見えるようになってくるでしょう。その際に「自分たちでメンテナンスできるシステムであること」がとても重要な要素となります。
自分たちで改善を行いたいと思っても結局システムがブラックボックスで何もできないということであれば、業者に委託して改良してもらうにもお金がかかるということになります。そうなると使用する側が妥協するか、最悪の場合、導入が失敗ということで撤去されてしまう可能性もあります。
遠くにある工場の稼働率もリアルタイムで確認
IoTによる工場設備のネット接続は、リアルタイムでデータをクラウドサーバにアップしていきます。
遠隔地でも、現地の工場の状況を確認することができるようになります。
日進工業の例では、中国に設立した工場の設備稼働率などのデータもクラウドサーバにアクセスするだけで現在のデータも確認することができるようになりました。
今までであれば、現地との会議を行う場合、設備稼働率などをテーマにしたものであれば、人の手で集計したデータを基に行うことになるので、集計期間が必要でした。
これでは迅速な対応ができなかったり、会議を行う頃には状況が変わっている可能性もあります。
遠隔地での状況も、現地の工場の責任者とリアルタイムのデータを見ながら会議をすることもできるようになります。
まとめ:効率アップのために先入観を捨てて考える
前回の記事のようにアイデア次第で様々なことが考えられるのがIoTのいいところです。
導入にお金がかかる、と感じたのであれば、お金がかからずに同じ水準を達成できる方法を模索しましょう。
様々な仕様の機器が常に開発されており、安価な仕様で必要最低限の機能を持ったものもあります。
その中には低価格で同じ水準を達成できる機器も、探せばあるのではないでしょうか。
また、ある程度自分たちで構築することで導入後のメンテナンスも抵抗なく行うこともできるようになります。これは製造業全体にも言えることではありますが、ITなどの情報分野の業務は、基本技能の一つとなりつつあると言えます。
もちろん、導入後のデメリットも考えなければなりませんが、効率化できそうだと考えたらまず自分たちでやってみるということが、効率化やIoT化への第一歩と言えるでしょう。