最適な浸炭硬化と焼入硬化層深さについて
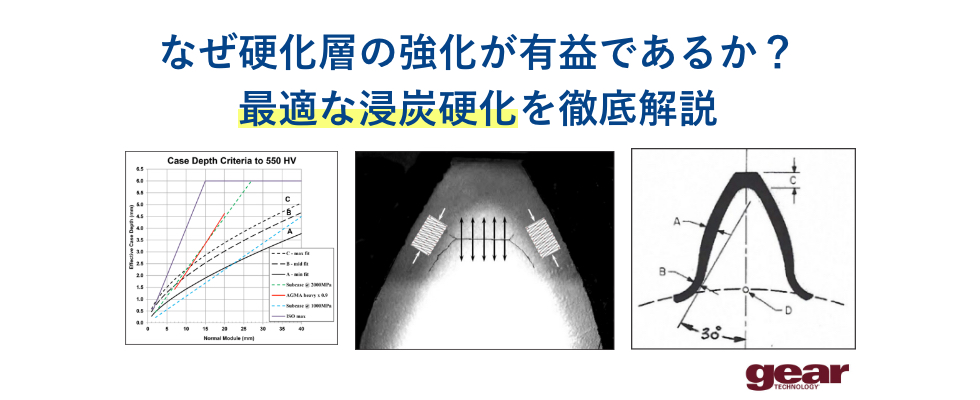
著者:Robert Errichello and Andrew Milburn 翻訳者:西部商工株式会社 瀬尾拓海
概要
歯車の*故障モードごとに浸炭硬化された最適な硬化深度は異なり、歯車の歯の異なる場所で定義する必要があります。現在の歯車定格基準は、さまざまな故障モードを完全に説明しておらず、考慮しなければならないさまざまな場所を明確に定義していません。 このホワイトペーパーでは、なぜ硬化層の強化が有益であるかを説明します。 さらに、異なる硬度値を使用して有効硬化深度(有効硬化層深さ)を定義し、推奨される値を提供します。 ISO 6336-5およびANSI / AGMA 2101-D04のギアレーティング規格、およびMAAGギアハンドブックに記載されているガイドラインに従って、硬化深度を計算および指定する方法に関連するリスクと比較します。そして、硬化深度を指定する必要がある3つの場所を示し、マイクロピッチング、サブケース疲労、曲げ疲労、硬化層/コア分離の破損モードを回避するために最適な硬化深度を決定するための個別の計算方法を示します。故障モードごとに、最小硬化深度があり、それを下回ると負荷容量が低下し、過度に深い場合は、耐荷重が低下、コストが増加し、その他の悪影響が及ぼされます。
前書き
この記事では、マイクロピッチング、サブケース疲労、曲げ疲労、硬化部/コア分離の故障モードについて、浸炭歯車の硬化深度について推奨しています。 故障モードの詳細については、ANSI / AGMA 1010(参照1)を参照してください。 ただし、各故障モードの最適な硬化深度は、歯車の歯の異なる場所で定義する必要があり、最適な硬化深度は故障モードによって異なります。 したがって、このホワイトペーパーでは、硬化深度を測定するための重要な場所を考慮して、各故障モードを個別に回避するために必要な硬化深度について説明します。 最適な硬化深度の概念の詳細については、参考文献2–3を参照してください。
効果的な焼き入れ硬化層の定義
有効硬化深度に関するヨーロッパの定義は、硬度が550 HV(約52.3 HRC)である硬化層内側の点から表面までの距離です。 この測定は、ビッカース微小硬度圧子を使用して行われます。 有効な硬化深度に関する米国の定義は、硬度が50 HRC(約513 HV)である硬化層内側のポイントから表面までの距離です。 この測定は、ヌープまたはビッカース圧子を使用して行われ、硬度値は、ASTM E140などの変換チャートを使用してHRCに変換できます。
完成した硬化深度が適切であることを保証するために、硬化深度を設計するときは、最大の研削代を考慮する必要があります。 したがって、典型的な図面仕様は、最終加工後の550 HVまたは50 HRCまでの有効硬化深度として定義されます。
米国の定義はヨーロッパの定義よりも深いことに注意してください。 残念ながら、硬度勾配の勾配は特定の歯車の寸法、材料の硬化性、および焼入れ速度を含む熱処理プロセスによって異なるため、2つの定義を簡単に変換する方法はありません。 したがって、2つの定義を比較するには、特定の歯車で実際の微小硬度勾配を測定して、50 HRC硬化深度が550 HV硬化深度と比較してどれだけ深いかを判断する必要があります。 一部の研究所は、この問題の解決に役立つように両方の深度を測定して報告します。 硬化深度の推奨事項はMAAGおよびISOガイドラインに基づいているため、有効硬化深度の550 HV定義がこのホワイトペーパーで使用されています。
全硬化深度の定義
全硬化深度は約1.5倍で、550 HV定義に基づいて有効硬化深度の2倍になる場合があります。 全硬化深度は、硬化層の炭素勾配が鋼合金のコア炭素含有量より0.04%高い深さとして定義されることがあります。
浸炭硬化深度測定の推奨場所
図1は、硬化深度の測定に著者が推奨する場所を示しており、D.W. Dudley氏に基づいています(参照4、図4.8)。 歯底フィレットでの硬化深度測定の位置を定義するために、30°の線が追加されました。
・歯の高さのほぼ中央にある場所Aは、フランクで硬化深度を測定する場所です。
・場所Bは、ルートフィレットで硬化深度を測定する場所です 。
・ 場所Cは、歯先での硬化深度を測定する場所です 。
・ 歯底円上の場所Dは、コアの硬度を測定する場所です 。
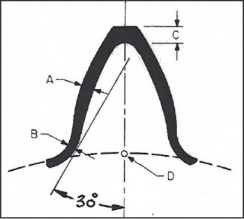
硬化深度を指定するときに考慮しなければならない故障モード以外の別の側面は、フランク、ルート、チップの位置で硬化深度が異なる可能性があるという事実です。 雰囲気熱処理(ガス浸炭)は、材料の硬化性、歯車の歯の形状、炉のパラメータ、焼入れパラメータなどのいくつかの要因に依存する硬化深度を生成するため、フランク、ルート、チップの硬化深度のばらつきは大きく異なります(時々同じ、時には全く異なる)。 通常、硬化深度は、ルートではフランクよりも少なく、フランクではチップ位置よりも少なくなります。 対照的に、真空浸炭はすべての場所でほぼ均一な硬化深度を生成できます。
硬化深度が歯車の歯の特性に及ぼす影響
浸炭の利点: 浸炭した歯車の歯は、表面が硬いため、マイクロピッチングおよび曲げ疲労に対する耐性が最大であり、浸炭すると、硬化層に有益な圧縮残留応力が生じます。 圧縮残留応力は、オーステナイトがマルテンサイトに変態するときの材料膨張の結果であり、負荷応力を効果的に低下させます。 ただし、硬化層の圧縮残留応力は、図に示すように、硬化層/コアの境界付近の有害な引張残留応力によってバランスが保たれます(図2)。

最適な硬化深度: 一般に、各故障モードでは、最小硬化深度があり、それを下回ると負荷容量が低下します(参照2–3)。 一方、極端に深い場合は、耐荷重が低下します(参照2–3)。 さらに、深い硬化は浸炭時間を長くする必要があり、これは次の理由で望ましくありません。
・粒間酸化(IGO)が増加し(特にMn、Cr、Siを含む合金の場合)、曲げ疲労耐性が低下します 。
・残留応力プロファイルが変更されます。これは、有益な圧縮残留応力が減少し、ヘルツ疲労耐性と曲げ疲労耐性の両方が減少するため、特に有害です 。
・粒子サイズが大きくなる可能性があり、ヘルツ疲労耐性と曲げ疲労耐性の両方が低下します 。
・硬化層が深すぎると、硬化層とコアの分離が促進されます 。
・歪みが大きくなるため、より細かい研磨材の除去が必要になります。
・製造コストが増加する可能性があります 。
お見積もり・お問い合わせはこちらから
マイクロピッチング
マイクロピッチングは、通常、非金属介在物などの表面下の欠陥で、歯の表面または表面の下の浅い深さで開始する可能性があります。 非金属介在物の影響を軽減するために、表面および硬化層内で高い圧縮残留応力を実現するために、有効硬化深度を設計することが重要です。 表1は、マイクロピッチングを回避するための最小有効硬化深度に関するいくつかのガイドラインを示しています。

2.有効硬化深度は50 HRCの定義に基づいています。
3.方程式についてはAを参照してください。
マイクロピッチングの推奨: 図3は、MAAGに基づいて著者が推奨した効果的な硬化深度を示しています(参照5)。 図3の導出、およびISO 6336-5(参照6)およびANSI / AGMA 2101(参照7)ガイドラインとの比較については、Bを参照してください。

図3の説明:図3の下の曲線「A」は、図の位置Aで測定された最小有効硬化深度です(図1)。 すべての機械加工が完了した後の硬化深度であり、歯面から硬度が550 HVになる深さまでの距離です。 最大のマイクロピッチング耐性を得るためには、曲線「A」が推奨されます。 ただし、設計者は、製造のばらつきに対応できるように硬化深度に許容差を設定する必要があります。 許容帯域幅は通常、ギアユニットのタイプ、それに課せられる条件、熱処理工場の設備、および熱処理結果の均一性に依存します。 曲線「B」と「C」は、曲線「A」で表される最小有効硬化深度に許容値を追加することによって得られる最大の硬化深度の許容範囲です。 曲線「C」は、商用ギアドライブ設計で通例の最大許容範囲を表しています。 曲線「B」は、精密ギアドライブ設計の許容範囲に適しています。
図3の曲線の方程式:
曲線A(heH)min = 0.2835(mn)0.7016(マイクロピッチングを回避するための最小値)
曲線B(heH)mid = 0.4730(mn)0.6198(最大精度許容値)
曲線C(heH)max = 0.5899(mn)0.5829(最大商業許容値)
サブケース疲労
※ヘルツ応力場内の接触面の下に亀裂が形成されることによる、表面硬化構成要素の破壊
「ケースクラッシング(浸炭層の広範囲の剥離)」という用語は、サブケースの疲労のために以前のギア命名法で誤って使用されていました。 ただし、サブケースの疲労は現在のところ優先される用語です。 詳細については、ANSI / AGMA 1010(参照1)を参照してください。
硬化深度、ヘルツ応力、残留応力、材料の疲労強度は、サブケースの疲労に影響します。 残留応力と疲労強度の表面下分布は、硬化層の硬度、硬化深度、およびコアの硬度に依存します。 硬化深度とコアの硬度の最適値は、残留応力と疲労強度の適切なバランスを提供し、サブケースの耐疲労性を最大化します(参照2–3)。
サブケースの疲労を防ぐには、最適な硬化層とコアの特性を得るのに十分な焼入れ性が鋼合金に必要です。 さらに、介在物が引張残留応力の領域で硬化層/コアの境界付近で発生すると疲労亀裂を引き起こす可能性があるため、清浄鋼を使用することが特に重要です(図2)。
運転中または製造中の歯車の歯の過熱(グラインドテンパーなど)は、硬化層の硬度を低下させ、残留応力を変化させ、サブケースの疲労に対する耐性を低下させます。 実際、グラインドテンパーは、サブケースの疲労破壊の根本的な原因であることがよくあります。 表2は、サブケースの疲労を回避するための最小有効 硬化深度のガイドラインを示しています。

2. Eq 43のUH = 44,000 N / mm2は、硬化深度=最大せん断応力までの深さの3.2倍に基づいています。
サブケース疲労推奨: AGMAガイドラインは上述の理由のために深すぎると著者の意見です(詳細については、参考文献2および3を参照してください)。 したがって、5.6.2.c節のISO 6336-5(参照6)の式を使用することをお勧めします。これは、Aに記載されており、便宜上、ここでは式1として繰り返されます。
ここで、ISO品質グレードMQおよびME(AGMAグレード2および3)ではUH = 66,000MPa、品質グレードML(AGMAグレード1)ではUH = 44,000MPaです。式1は、硬化深度の550 HV定義に基づいており、側面(場所A)に対するものであることに注意してください。ヘルツ応力σHは、実際に使用中に加えられる最大応力と等しくなければなりません。衝撃荷重が大きいアプリケーションの場合、必要な最小有効硬化深度は、曲線A(図3)で示されるものよりも大幅に高くなる可能性があります。したがって、σHは慎重に選択する必要があります。極端に深い場合は、マイクロピッチング耐性と曲げ疲労耐性の両方が低下するためです。これには、適用された荷重による強度、残留応力、および表面下のヘルツ応力勾配の分析が必要です。

図4は、参照用に追加された2つの異なる接触応力数と追加の線における推奨サブケース疲労基準に基づく有効硬化深度を示しています。サブケース疲労計算に使用される歯車の形状を示します(表3)。 AGMAの太い線に0.9を掛けて、50のHRC定義から硬化深度の550 HV定義に調整しました。

表3は、図4のサブケース有効硬化深度極座標グラフの計算に使用される歯車対の諸元と、図7のピニオンのトップランド厚さを使用した最大有効硬化深度の極座標グラフを示しています。

曲げ疲労
浸炭は正味引張曲げ応力を低減する圧縮残留応力を誘発するため、浸炭による表面硬化は特に有益です。 さらに、ショットピーニングを使用して、ルートフィレットの表面の圧縮残留応力を強化できます。 浸炭歯車の場合、硬化層の硬度、硬化深度、およびコアの硬度には最適値があり、残留応力と疲労強度の適切なバランスを提供して、曲げ疲労への耐性を最大化します(参照1–3)。 曲げ疲労を回避するための最適な硬化深度は、マイクロピッチングを回避するための最適な硬化深度よりも小さいことに注意してください。 したがって、フランク硬化深度に加えて、ルート硬化深度を測定することが重要です。 表4は、曲げ疲労を回避するための最小有効硬化深度に関するいくつかのガイドラインを示しています。

2. 参考文献6には、「長寿命に対する許容曲げ応力に関連する最適な有効硬化深度として、歯の仕上げ後、ルートフィレット上法線にtan30°で:0.1–0.2(mn)」と記載されています。
3. 参考文献7では、グレード2の場合は歯の高さの1/2で最小指定硬化深度の50%、グレード3の場合は66%を推奨しています。
曲げ疲労推奨: 図5は、曲げ疲労を回避するために著者が推奨する最小硬化深度を示しています。 曲げ疲労を回避するための最適な硬化深度については、図5の導出とISO 6336-5(参照6)ガイドラインとの比較については、Cを参照してください。
図5曲線の式:(heF)min = 0.2016(mn)0.7994

お見積もり・お問い合わせはこちらから
表面下で発生する曲げ疲労
古典的な曲げ疲労破壊は、歯の張力側のルートフィレットの表面で始まります。ただし、ルートフィレットのかなり上の位置で曲げ疲労亀裂が発生し、公称曲げ応力がルートフィレットよりもはるかに低い場合、破損の根本的な原因は非金属介在物などの材料の欠陥である可能性があります。 アルミン酸カルシウムなどの硬くて変形しない介在物は、鋼よりも熱膨張係数が低く、焼入れ熱処理の結果として、各介在物の周りに集中して引張残留応力が発生します。介在物からの引張残留応力と、硬化層/コア境界の下にある既存の引張残留応力は、加えられた荷重からの公称曲げ応力に追加されます。したがって、非金属介在物は、亀裂の起点の位置をルートフィレットの表面から硬化層/コア境界または他の領域の下に移動させる可能性があります。その結果、非金属介在物は多くの場合、硬化層/コア境界の下の地下位置で始まる曲げ疲労亀裂の根本的な原因です。通常、亀裂は、引張残留応力が高い領域の有効硬化深度の約2.5倍の深さにある非金属介在物から始まります(図2)。有効硬化深度が深いほど、表面から遠くなるほど、潜在的に損傷を与える引張残留応力のピークが発生します。この関係は、加えられた応力が表面からの距離とともに減少するという事実とともに、コア/コア境界の近くで疲労破壊が発生する可能性を減らします。現在、表面下で発生する曲げ疲労のリスクを評価するための工業規格はありません。ただし、ISO / DTS 6336-4(参照8)は、故障モードに対処するために現在開発中のドラフト技術仕様です。
硬化層/コアの分離図6は、浸炭した歯車の歯の先端近くの硬化層/コアの境界の下に発生した硬化層/コアの亀裂を示しています。硬化層とコアの分離は、硬化層の圧縮残留応力が、歯先での硬化深度が過度に大きいために、歯先近くのコアの引張強度を超えると発生します。内部の亀裂が伝播し、コーナー、エッジ、または歯の先端全体が分離する可能性があります。亀裂は、熱処理の直後、その後の取り扱いまたは保管中、または使用時間の後に現れる可能性があります。引張残留応力が高く延性が低いと、脆性破壊が起こり、歯先が爆発的に分離することがあります。条件がそれほど厳しくない場合、亀裂が歯の表面に到達する前に停止する可能性があります。介在物は、硬化層/コアの分離を促進します。特に、引張残留応力の領域で硬化層/コアの境界付近に発生する場合(図2)。水素は介在物に蓄積し、脆性破壊を引き起こす可能性があります。使用中の応力により、疲労により亀裂が成長する可能性があります。過度の硬化深度を防ぐために浸炭中に炭素の浸透を制限するために狭いトップランドを避けるか、銅プレートでトップランドをマスキングすることにより、硬化層/コア分離のリスクを減らすことができます。

硬化層とコアの分離は、脆性破壊です。 したがって、硬化層とコアの分離を回避するには、材料の破壊靭性を高くすることが重要です。 最高の靭性特性は、コア硬度が30〜40 HRCの範囲の3%NiCrMo鋼で得られます。 真空溶解鋼を使用し、炭素、リン、硫黄の含有量をできるだけ低く保つことで、靭性を最大化できます。 詳細については、AGMA 1010(参照1)を参照してください。 表5は、硬化層/コアの分離を回避するための最大の効果的な硬化深度に関するいくつかのガイドラインを示しています。 残念ながら、ISO 6336(参照6)とAGMA 2101(参照7)の間には矛盾があり、どちらも歯の側面で最大有効深さ0.4(mn)を許容しますが、Dudley(参照4)とAGMA 911(参照 9)歯先での最大有効硬化深度0.4(mn)を推奨します。

2. 参照6では、歯の中央高さの位置Aで最大有効硬化深度0.4(mn)、または最大6 mmが許容されます。
3. 参考文献7では、歯の中央高さの位置Aで、最大有効硬化深度0.4(mn)または通常のトップランド厚さ56%のうち、どちらか小さい方が許容されます。
4. 参考文献9は次のように述べています。「硬化層は、歯の先端とエッジが脆くなるか、コアに高い残留引張応力が発生するほど大きくてはなりません。 歯先の最大硬化深度は、歯のトップランド厚さ56%に制限する必要があります。」
硬化層/コア分離の推奨: 硬化層/コア分離故障モードでは、歯先の硬化深度が重要です。 したがって、著者らは、歯の先端(図1の位置C)での550 HVまでの最大有効硬化深度を(heT)max = 0.40(mn)またはトップランドの厚さの56%のどちらか小さい方に制限することを推奨しています。 図7は、ピニオンチップの厚さの0.56倍という基準に基づくラインを示しています。 現在、この基準は550 HVまでの深度に基づいていますが、現在のAGMA 2101は50 HRCまでの深度に基づいて同じ基準を使用しています。 表3に要約されている諸元を使用して、3つの異なる歯車対に対して計算が行われました。図8は、このホワイトペーパーで説明する4つの故障モードすべての推奨硬化深度を示す要約プロットです。
結論
有効硬化深度は、それが測定される場所によって異なる場合があるため、著者は、3つの異なる場所で指定することを推奨しています(図1)。各場所での最適な硬化深度は、検討している故障モードによって異なります。この記事では、いくつかの異なるソースからの硬化深度ガイドラインを比較し、4つの異なる故障モードに関する著者の推奨事項を示します。
A:効果的な硬化深度命名法の方程式:
ルート命名法:
(heF)min = 曲げ疲労に基づく仕上げ後のAGMAルートの最小有効硬化深度は50 HRCまで。
(heF)min =曲げ疲労に基づいて仕上げた後のDudleyルートの最小有効硬化深度は50 HRCまで。
(heF)min =曲げ疲労に基づいて仕上げた後のMAAGルートの最小有効硬化深度は550 HVまで。
(heF)opt =曲げ疲労に基づく仕上げ後のISOルート最適有効硬化深度550 HV。
フランク命名法:
(heH)max =マイクロピッチングに基づく仕上げ後のMAAG逃げ面最大(商業的許容差)有効硬化深度は550 HVまで。
(heH)mid =マイクロピッッチングに基づく仕上げ後のMAAG逃げ面最大(精度許容差)有効硬化深度は550 HVまで。
(heH)min =マイクロピッチングに基づく仕上げ後のAGMA側面の最小有効硬化深度は50 HRC(通常負荷および重負荷硬化深度)まで。
(heH)min =マイクロピッチングに基づく仕上げ後のMAAG逃げ面の最小有効硬化深度は550 HVまで。
(heH)opt =マイクロピッチングに基づく仕上げ後のISOフランク最適有効硬化深度550 HVまで。
(heS)min =サブケースの疲労に基づく仕上げ後のAGMA逃げ面の最小有効硬化深度は50 HRCまで。
(heS)min =サブケースの疲労に基づく仕上げ後のISOフランクの最小有効硬化深度550 HVまで。
チップ命名法:
(heT)max =硬化層/コアの分離に基づく仕上げ後、AGMAチップの最大有効硬化深度は、50 HRCまで。
(heT)max =硬化層/コアの分離に基づく仕上げ後、Dudleyチップの最大有効硬化深度は50 HRCまで。
フランク硬化深度の方程式
AGMA 2101(参照7)図13(フランク50 HRC):
通常負荷硬化深度
AGMA 2101(参照7)サブケース疲労方程式(43)に基づき、UH = 44,000 MPa:(heS)min = [σHdw1 sin(αwt)/ UH cos(βb)] CG
ISO 6336-5(参照6)図17最適なケースの奥行き(フランク550 HV):
(heH)opt = CHDH,opt = 0.15(mn)モジュール範囲2≤mn≤10(heH)opt = CHDH,opt = 0.083(mn)+ 0.67モジュール範囲10 <mn≤40
ISO 6336-5(参照6)サブケース疲労方程式(5.6.2.c)に基づき、品質グレードMQ / MEの場合はUH = 66,000 MPa、品質グレードML(フランク550 HV)の場合はUH = 44,000 MPa:
(heS)min = [σHdw1 sin(αwt)/ UH cos(βb)] CG
MAAG(参照5)経験式方程式(6.422)(フランク550 HV):
(heH)min = (mn / 2 + 1.1) ½– 1
MAAGに適合した曲線の方程式(参照5)図6.12(付録Bを参照)(フランク550 HV):
(heH)min = 0.2835(mn)0.7016(マイクロピッチングを回避するための最小)
(heH)mid = 0.4730(mn)0.6198(最大精度許容差)
(heH)max = 0.5899(mn)0.5829(最大商用許容差)
ルート硬化深度の方程式
AGMA 2101(参照7)表9(ルート50 HRC):
(heF)min = 0.50(heH)min(グレード2)
(heF)min = 0.66(heH)min(グレード3)
ISO 6336-5(参照6)最適な硬化深度方程式(5.6.2.b)(root 550 HV):
(heF)opt = CHDF,opt = 0.10(mn)から0.20(mn)
Dudley(参照4)最適な硬化深度方程式 (4.2.a)(ルート50 HRC):
(heF)min = 0.16(mn)
MAAG曲げ疲労を回避するための最小硬化深度(Cを参照)(ルート550 HV):
(heF)min = 0.2016(mn)0.7994
チップ硬化深度方程式
Dudley(参照4)最大硬化深度方程式 (4.4.a)(チップ50 HRC):
(heT)max = 0.4(mn)
ISO 6336-5(参照6)最大硬化深度方程式(5.6.2.d)(フランク550 HV):
(heT)max = CHDmax = 0.4(mn) (≤6 mm)
AGMA 2101(参照7)最大硬化深度方程式 (44)(フランク50 HRC):
(heT)max = 0.4(mn)または0.56(tno)の小さい方
B:図3の導出
MAAGガイドライン: 図B-1は、オリジナルのMAAG [5] 図6.12を示しています。

図3の導出に使用された方法
次のテキストと図B-2は、このレポートの図3の導出に使用された方法を説明しています。
・ 図B-2の下の緑色の線は、MAAG(参照5)の式に準拠しています:(heH)min =(mn / 2 + 1.1)½-1
・ 下の赤い線は、MAAG方程式のExcelパワーカーブフィットで、ここではMAAG_min_fitとして再定義されています。
・ 上部の緑色の線と中央の青色の線は、MAAGの上部と中央の曲線から得られました(参照5)図6.12。 これらの2つの線に方程式が与えられていないため、値は図6.12から手動で読み取られました。
・ 上部の赤い線と中央の黒い線は、それぞれ上部の緑の線と中央の青い線のExcelパワーカーブフィットです。
・ 下の青い線は、上の緑の線と下の緑の線の違いを表しています。 下の青い線はモジュールの増加に伴って着実に増加しないことに注意してください。 これにより、Excelのパワーカーブは、最終的な上部と下部の赤い線を滑らかにするために適合しました。
・ 紫色の線は、上部の赤い線と下部の赤い線の違いを表しています。 紫色の線はモジュールの増加に伴って着実に増加していることに注意してください。




MAAG、ISO 6336-5、およびAGMAガイドラインの比較
図B-3は、マクロピットを回避するための最小有効硬化深度を550 HVにするためのMAAGmin_fit(参照5)(黒い線)とISO 6336-5(参照6)の最適(赤い線)ガイドラインを比較しています。 MAAGガイドラインには、成功した適用の長い歴史があります。図B-3は、MAAGmin_fitとISOのガイドラインが8〜25の通常モジュールの範囲で非常に似ていることを示しています。 8未満のモジュールの場合、MAAGmin_fitガイドラインはより深い硬化深度を推奨し、25を超えるモジュールの場合、ISOガイドラインはより深い硬化深度を推奨します。 AGMAの通常負荷の硬化深度(青色の線)、重負荷硬化深度(緑色の線)、およびISO最大線(紫色の線)も含まれます。青と緑の実線は、青と緑の破線に0.9を掛けて、AGMAガイドラインを50 HRC定義から硬化深度の550 HV定義に調整することで得られました。 AGMA 2101重負荷ガイドラインが10を超えるモジュールのMAAGmax_fit許容範囲よりも大幅に深いのは明らかですが、一方、AGMA 2101の通常のガイドラインは、最大マクロピッチング抵抗のMAAGmin_fitガイドラインに似ています。50HRC硬化深度が550HV硬化深度よりも深いことを考慮してください。 実際の硬度勾配に関するデータがないと、50 HRC定義と550 HV定義に基づいて硬化深度さを正確に比較することができないことに注意してください。したがって、図B-3に示す比較は定性的なものにすぎません。
C:図5の導出
最大の曲げ疲労耐性を得るために図5を導出するために使用された方法
次のテキストと図C-1およびC-2は、図5の導出に使用された方法を説明しています。図C-1に示されている線は次のとおりです。
・ 上部の線は、曲げ疲労抵抗の最大ケース深さのISO方程式(heF)opt = 0.2(mn)に準拠しています。
・ 次の行は、最大マイクロピッチング抵抗(heF)min = 0.2835(mn)0.7016のMAAG最小硬化深度に準拠しています。
・ 赤い線は、式(heH)min = 0.2016(mn)0.7994で定義される最大曲げ疲労抵抗の硬化深度です。この線は、最大マイクロピッチング抵抗の場合はMAAG最小硬化層/深さよりわずかに低く、最大曲げ疲労抵抗の場合はISO制限0.1(mn)≤(heF)opt≤0.2(mn)内に選択されました。
・ 赤い線の下の線は、曲げ疲労抵抗の最小硬化深度のISO方程式(heF)opt = 0.1(mn)に準拠しています。
・ 下の2つの線は、曲げ疲労耐性の最小硬化深度のAGMA 2101方程式に準拠しています。
グレード2の場合、¤(heF)min = 0.50(heH)min(MAAGの50%適合)
グレード3の場合、¤(heF)min = 0.66(heH)min(MAAGの66%適合)
図C-2は、図C-1のmn≤10の拡大図です。これは、最大曲げ疲労抵抗の式(heF)min = 0.2016(mn)0.7994が、0.1(mn)≤(heF)opt≤0.2(mn)のISO限界のほぼ中間の硬化深度を与えることを示しています。
参考文献
1. AGMA, 2014. “Appearance of Gear Teeth – Terminology of Wear and Failure,” ANSI/AGMA 1010- F14.
2. Parrish, G. 1999, Carburizing: Microstructure and Properties, ASM International, Materials Park, OH.
3. Doane, D.V. 1990, Modern Carburized Nickel Alloy Steels, Nickel Development Institute, Toronto, Ontario, Canada.
4. Dudley, D.W. 1984, Handbook of Practical Gear Design, McGraw-Hill, New York, NY.
5. 1990, MAAG GEAR BOOK. MAAG Gear Company, Zurich, Switzerland.
6. ISO, 2015. “Calculation of Load Capacity of Spur and Helical Gears — Part 5: Strength and Quality of Materials,” ISO 6336-5.
7. GMA, 2004. “Fundamental Rating Factors and Calculation Methods for Involute Spur and Helical Gear Teeth,” ANSI/AGMA 2101-D04.
8. ISO, 2017. “Calculation of Load Capacity of Spur and Helical Gears — Part 4: Calculation of Tooth Flank Fracture Load Capacity,” ISO/DTS 6336-4.
9. AGMA, 1994. “Design Guidelines for Aerospace Gearing,” AGMA 911-A94.
Robert Errichello(PE)は、自身のギアコンサルティング会社(GEARTECH)を率いており、GEARTECH Software Inc.の創設者です。カリフォルニア大学バークレー校を卒業し、機械工学の学士号と修士号、および工学の修士号を取得しています。構造ダイナミクス。エルリチェロは50年以上の産業経験の中で、いくつかのギア企業で働いていました。彼は40年以上にわたって歯車業界のコンサルタントを務めており、サンフランシスコ州立大学とカリフォルニア大学バークレー校で材料科学、破壊力学、振動、機械設計のコースを教えてきました。彼はまた、ASMインターナショナル、STLE、ASMEパワートランスミッションおよびギアリング委員会、AGMAギアレーティング委員会、AGMA / AWEA風力タービン委員会のメンバーでもあります。 Errichelloは、歯車の設計、解析、および応用に関する100を超える記事を発表しており、歯車の設計と解析に広く使用されている3つのコンピュータプログラムの著者です。彼はまた、Gear Technology誌とSTLE Tribology Transactionsで長年の技術編集者を務めており、歯車の設計、分析、潤滑、故障分析に関する数多くのセミナーを開催しています。 Errichelloは、AGMA TDECアワード、STLE Wilbur Deutch Memorialアワード、AGMA Lifetime Achievementアワード、EP Connellアワード、STLE Bissonアワードの過去の受賞歴があります。
Andy Milburnは現在、ワシントン州タコマの近くにあるコンサルティング会社であるMilburn Engineering Inc.の社長であり、ギアとギアボックスの設計と解析で45年の経験があります。 1989年に自身のコンサルティング会社を設立する前は、ワシントン州シアトルのThe Gear Worksに15年間勤務し、ギア製造、ギア故障分析のすべての側面に関与し、多くのカスタム産業用ギアボックスを設計しました。コンサルタントとして、ギアとベアリングの多くの故障を調査し、クライアントがギア製品を改善するのを支援しました。過去18年間、彼は風力発電業界でギアボックスの故障の調査、ギアボックスの修正の開発、およびデューデリジェンスの設計レビューへの参加に非常に積極的でした。彼はISO TC66の米国代表であり、新しい国際ギアボックス規格であるIEC 81400-4に取り組んでいました。彼はワシントン州で登録されたプロフェッショナルエンジニアであり、AGMA、ASME、ASM、STLEのメンバーであり、AGMAヘリカルギアレーティング委員会のメンバーです。ミルバーンは現在、AGMAギア故障解析コースのモデレーターの1人です。
*故障モード(こしょうモード、英: failure mode)は、JIS C5750-4-3:2011では「アイテムにおける故障の様子」と定義されている。JIS Z8115:2000のF2では「故障状態の形式による分類。例えば、断線、短絡、折損、摩耗、特性の劣化など」と定義されている。 故障モードは、ハードウェアの部品の構造に着目したもの、機能に着目したもの、工程に着目したものなどに分類される。[引用先:Wikipedia]
現場でお困りの方を
徹底的にサポートします!
ソリューション、製品に関する
お見積もり・お問い合わせはこちらから
まずは、お気軽にご相談ください!
当社への貴社商品・サービスのご紹介営業につきましては、お問合せ・ご相談フォームにてご連絡下さい
- お電話の方はこちらから
受付時間 : 9:00-17:00(平日) - TEL078-335-7573